Content
Accelerate assembly with an industrial robot
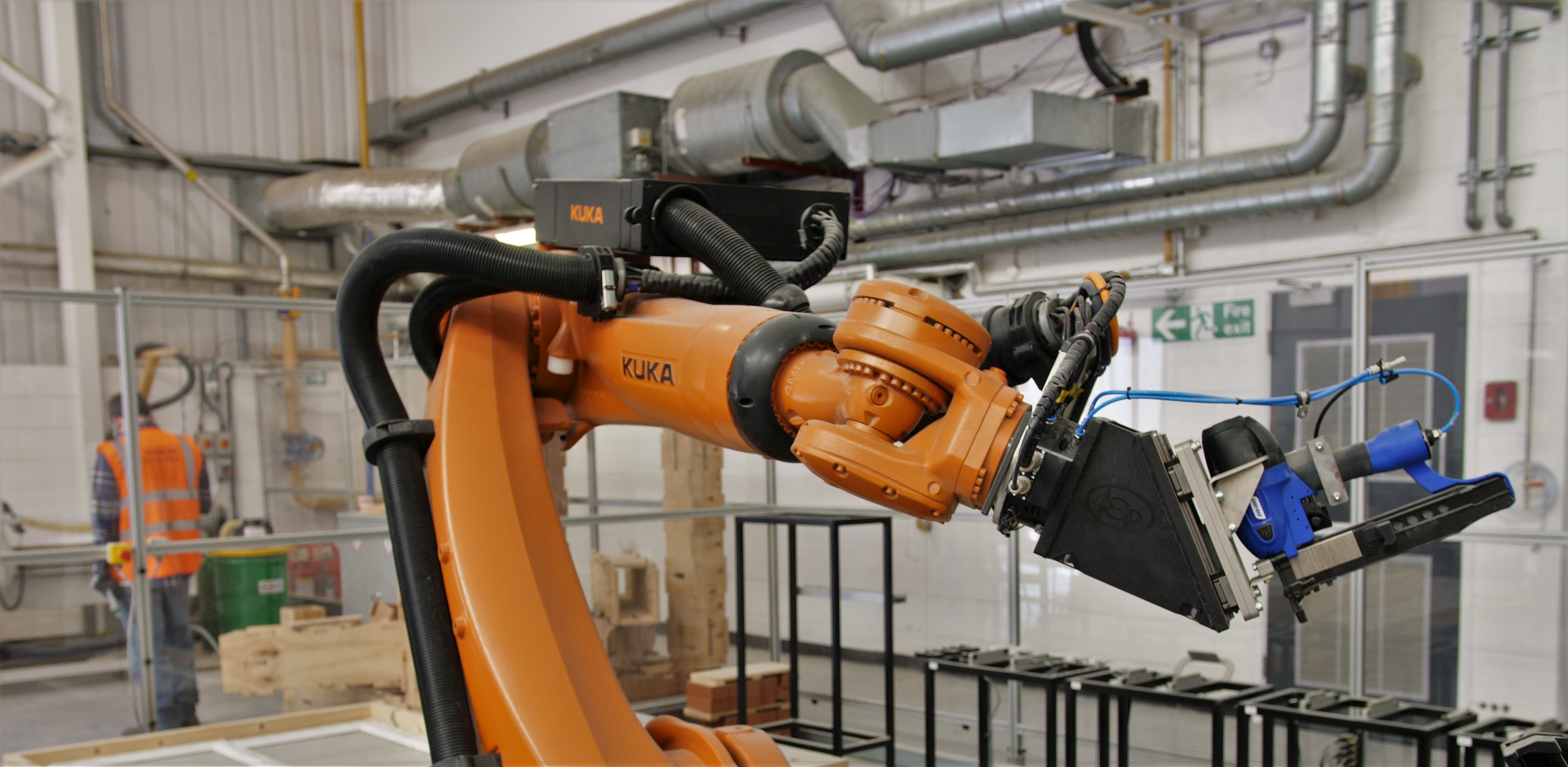
Robotics is on the rise. And BE-ST's industrial robot is helping by bringing accelerated offsite assembly into reality as one of Scotland’s construction companies (unnamed) shortened a normally lengthy process to just a few minutes.
BE-ST bought its industrial robot back in its early years as part of its core funded equipment, seeing the equipment as part of the vision of a future smart factory for construction.
That vision was looking into the future, as at the time, no known companies in Scotland were effectively utilising robotics for construction.
Now the robot is helping feed into the realisation of that vision as it has helped inform the strategy of one construction company, who indicated that it would look to invest in similar equipment in the future after successfully trialling a new process with it.
Our robot
BE-ST originally invested in the robot in 2017.
In 2020 BE-ST invested in a further array of tools to help expand its capabilities even further.
This kind of robot would sit in a factory environment as part of a manufacturing line to quicken speed, improve accuracy, reduce Health and Safety considerations, and reduce error in processes.
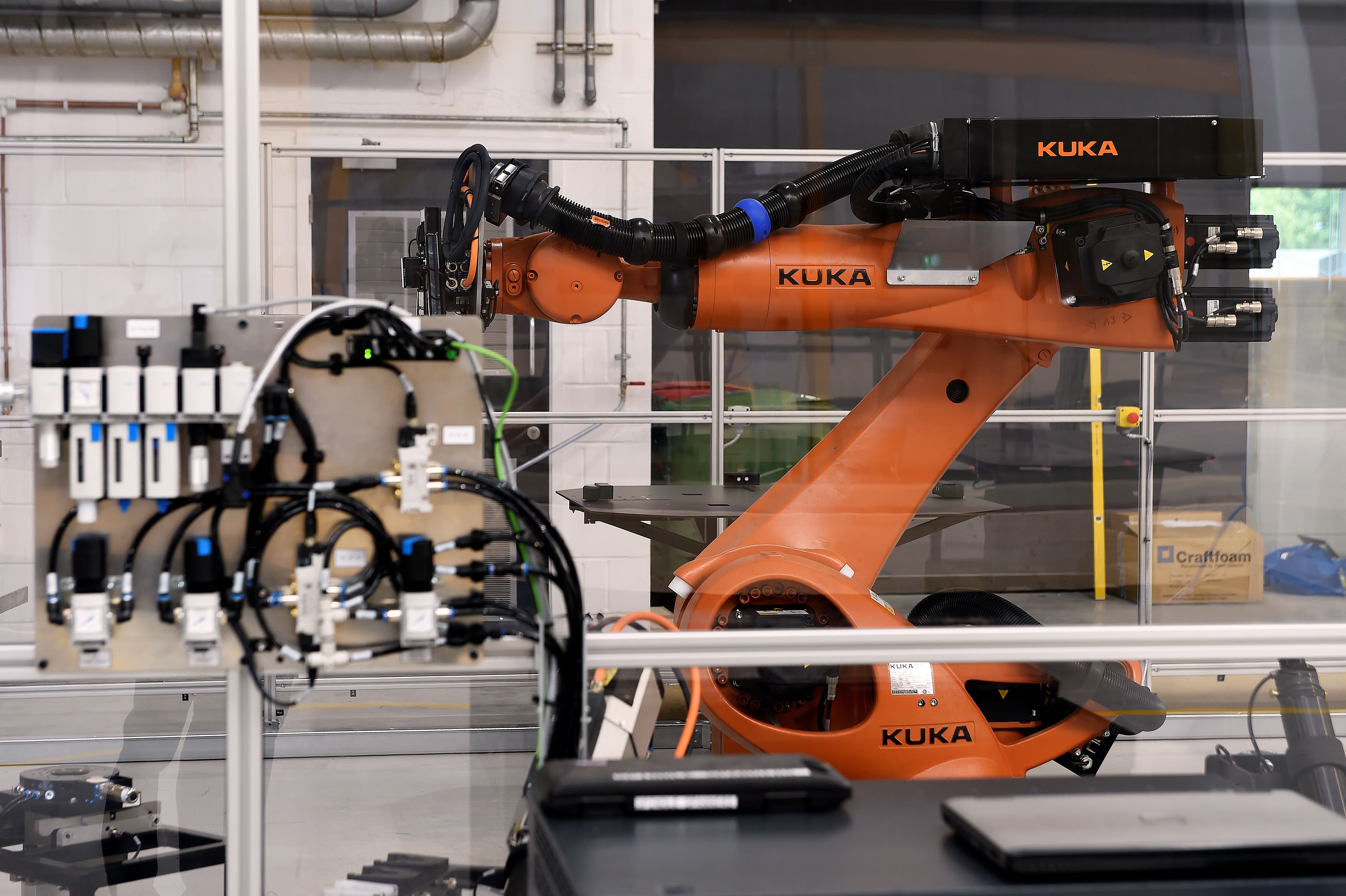
The robot arm itself can lift 210kg and has a 2.6m long x 1.5m wide pick and place vacuum array end effector with suitable contact and adhesion to handle up to 120kg.
It can operate handheld power tools with sequential triggers allowing automation of various power tools such as Nailers and staplers.
It also has an end effector with a circular saw blade. This allows you to use the robot as a cutter to aid in the production of components or panelised solutions.
The robotic arm has 6-axis of movement and alongside an external 7th axis can work at almost any angle and process material on all sides and surfaces.
The project
Our factory is a place for ideas to come to life. And the industrial robot here at BE-ST has now helped do just that.
Technologies of this scale need research to back a decision of investment. But often the testing and researching requires large scale investment in itself if companies are to do it on their own - a catch 22 that many construction organisations face when looking to innovate. And that’s where BE-ST can come in to help.
We help companies improve their sustainable and commercial outlook by helping them do or create something new. A large part of this involves de-risking innovation by allowing companies to trial and test new manufacturing approaches without the same hefty financial or resourcing drawbacks.
On this project, we worked with the clients to scope out a new offsite manufacturing process using our industrial robot, giving access to the robot itself, knowledge of its use and input into the process from start to finish.
The learnings from this project can allow industry to scale up and investment in technology, with more confidence and surety around future investment justifications and ROI business case.
BE-ST funding for procurement and use of all equipment, derisked the project and ensured industry engaged. Client
The new process, usually done onsite at a far slower pace, can now be done in 2 minutes with the robot.
These proof of concept trails have proven that using an industrial robot can dramatically reduce a time intensive process significantly, that it would not reduce factory output and that the new process is possible, effective and scalable. It also showed that the process can be done for less cost than installation on site. Using an industrial robot elimiated certain manual factory systems, reduced manual handling, and improved accuracy, output rates, and quality of the final product.
The work in the innovation factory helped provide the key considerations, the necessary specifications and the justifications to decide on whether to invest in similar equipment.
Knowledge was transferred between [client] and BE-ST, fast-tracking industry learning and know-how in low risk, safe and efficient collaborative way. Client
The impact
88% of businesses worldwide plan to adopt robotic automation into their infrastructure.[1]
What are the benefits?
- Mitigate H&S risks;
- Increase production capacity;
- Reduce labour demand;
- Reduce risk of damage to windows from manual handling and subsequently reduce waste;
- Provide an audit trail of correct installation;
- Increase product quality.
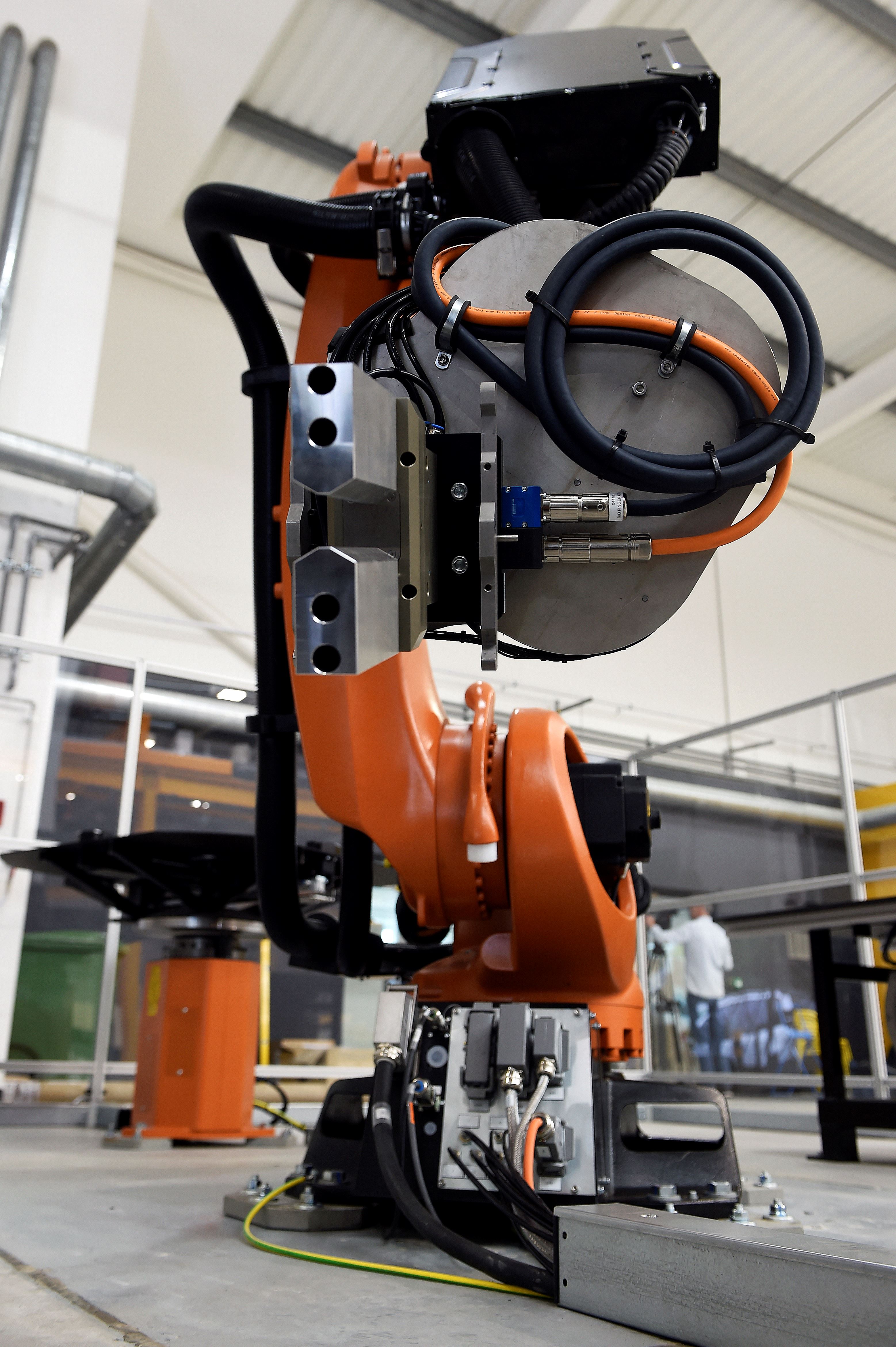
How did working with BE-ST help?
According to the client, the project wouldn’t have been possible without BE-ST.
For them the benefits of working with BE-ST brought about many new learnings and outcomes:
- “Using the BE-ST Innovation factory to trial new manufacturing approaches, outwith using our own facilities, negated the impact on delivering day to day production demands.
- Using the BE-ST equipment eliminated the need for investment in unproven technology, which would have killed the project and resulted in ourselves not proceeding the project.
- Using the BE-ST / ENU skills base allowed access to robotic programming and configuration skills/expertise and know-how, without need for specialist 3rd party consultants or steep/risky industry learning curve.
- Knowledge was transferred between [client] and BE-ST, fast-tracking industry learning and know-how in low risk, safe and efficient collaborative way.
- BE-ST funding for procurement and use of all equipment, derisked the project and ensured industry engaged
- The know-how, learnings and IP generated remained with the client and can be utilised with commercial technology partners to allow industry scaling up and investment in technology, with more confidence and surety around future investment justifications and ROI business case.”
The project has shown how effective utilising robotics for construction can be. But the story doesn’t stop there: the use of robotics has a lot to offer the sector as institutions like the National Robotarium bring new robotics use-cases to light.
Run by the University of Edinburgh and Herriott Watt, the recently opened centre is another step closer to having a joint-up ecosystem of players in this space innovating and using robotics for good.
- 88% of businesses worldwide plan to adopt robotic automation into their infrastructure
- Largest size window and door sets can be lifted & positioned
- 2 minutes to complete new process
- Reduction of onsite labour
- Lowered cost of installation
- Reduced site transport
- Reduced Site Health and Safety risk
Yes. Companies can work on one-off projects or work commercially with our Industrial robot. Learn more and get in touch with our team to see how we can help.