Content
The Tardis: A test bay for thermal and airtightness testing
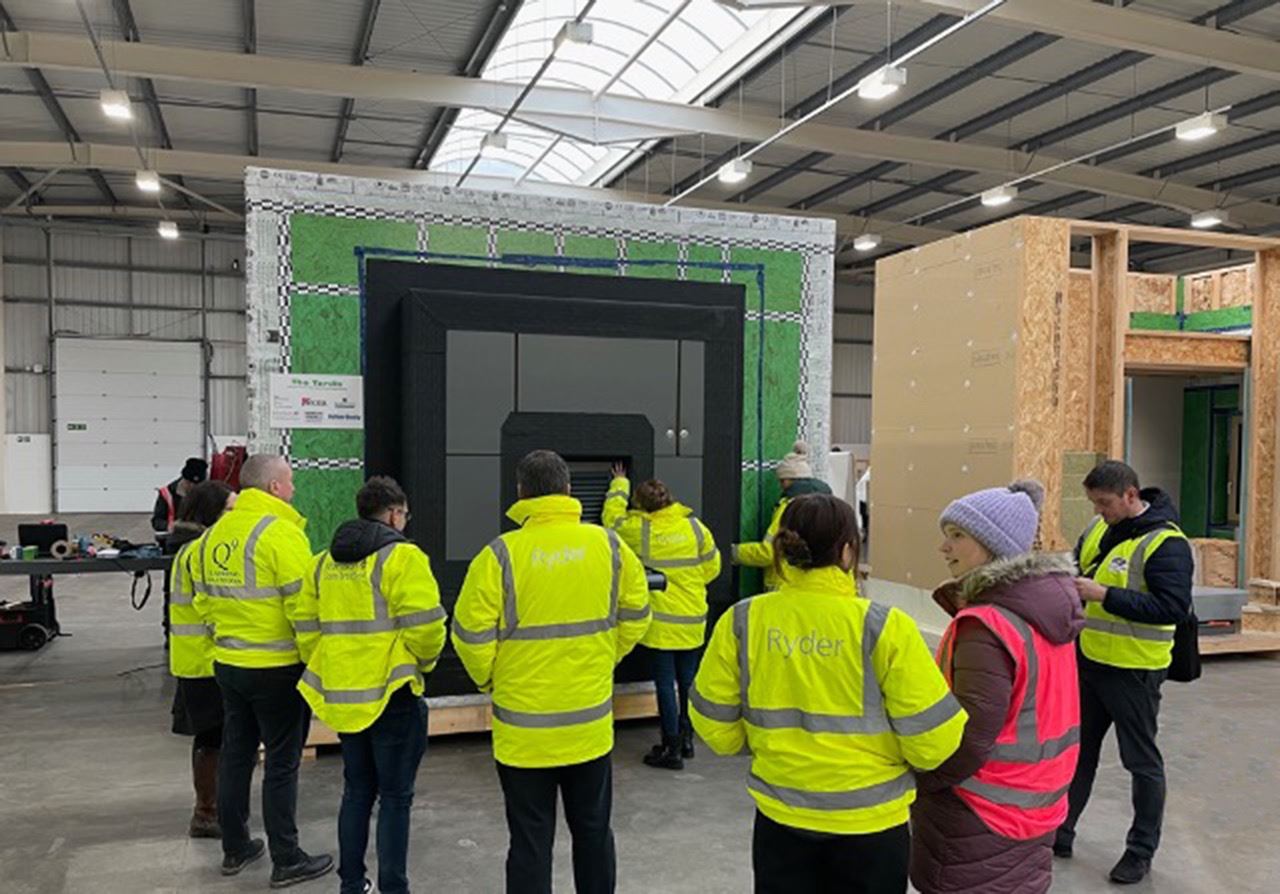
Tier 1 Contactors (T1C) are traversing the Passivhaus space and bringing industry along with them, all inside this mysterious box.
T1C collaborators Morrison Construction, Kier Construction, Balfour Beatty, Robertsons and Morgan Sindall, their supply chains and BE-ST, has built a box in BE-ST’s factory, aptly called the Tardis as there is more to it than meets the eye.
The new test bay has been developed to learn more about thermal principles and airtightness in practice, to test new processes, products, and methods so that the T1C collaborators, other members of the industry and their supply chain can improve their build-ups and knowledge-base when delivering Passivhaus projects.
Background
The Steel Test Rig project that Morrison Construction built in collaboration with BE-ST experimented with different detail build-ups on a steel frame Passivhaus. Following on from this, Allan Smith, who is leading on the project from Morrison Construction, says: “we discussed ideas with the other T1Cs and that got us speaking about how it would be really good if there was a central purpose-built test facility that we could do different types of detail build ups, that we could perform validated tests on.”
Kier Construction’s Stephen Booth designed the layout of the latest, larger scale test rig with assistance from Architype and Goodsons Associates.
The original concept was born at St Sidwell’s Point project where Stephen designed and developed a small airtight rig, the size of a telephone box (fondly referred to as the ’Testing Tardis)’ with an interchangeable front to test the impact different fixing types had on the airtightness performance of the primary external wall build up.
Stephen explained: ”the larger volume of the next generation Tardis will allow formal air testing to be carried out using a calibrated blower door fan and can be supplemented by other test methods and tools such as thermography and smoke machines to assist with providing useful, visible indicators of expected performance.”
“The ‘Tardis’ will provide a useful upskilling and educational tool for carrying out practical, hands-on training, quality benchmarking and an opportunity to visually illustrate the impact of ‘good’ and ‘bad’ detailing and workmanship.”
“It will also enable real life data to be gathered to assist with establishing the true performance, robustness and buildability of bespoke construction details, key junctions, interfaces, systems, materials, components, which hopefully can be used to further inform and develop a suite of simplified and standardised approaches.”
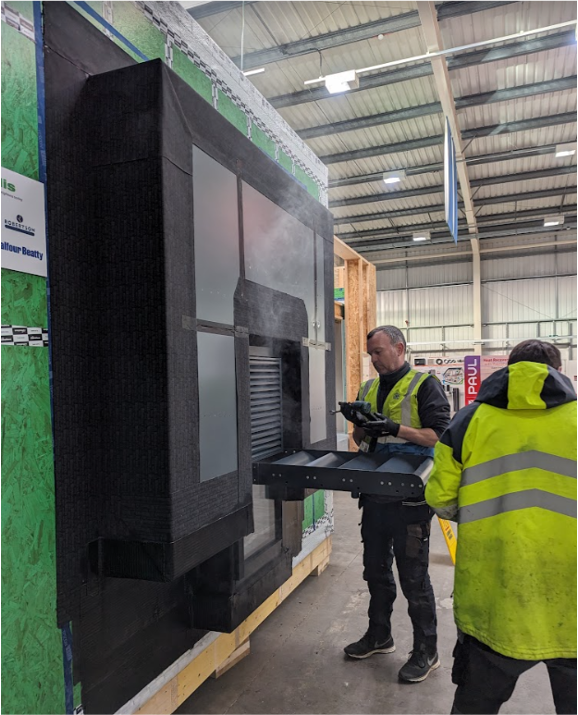

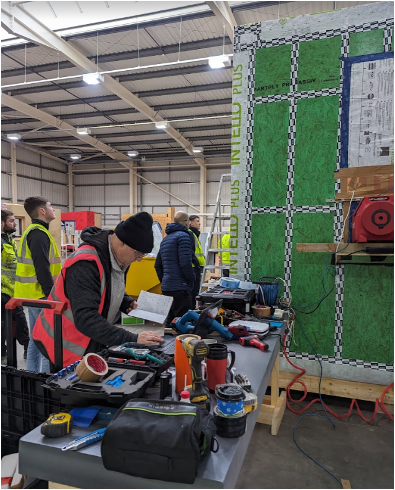
The Tardis in-action
Morrison Construction wanted to include industry in the delivery from the start, so they had their supply chain help deliver the project. The base rig was built by Ecosystems Technologies, while other sub-contractors and suppliers, including Q9, Castle Building Services, Kingspan, Linn-Tech, and Fleming Timber, provided materials and expertise for the facility's construction.
The Tardis is designed to be used for a series of tests on different construction details and materials. These tests included smoke testing, air testing, and validation tests to ensure compliance with airtightness standards.
Morrison Construction has been first to utilise the Tardis, and is actively using the insights gained from the Tardis facility on their upcoming Passivhaus projects: “We've got two major Passivhaus projects on the go at the moment. Our Faifley Campus and Paisley Grammar campus, which use the same kind of details and we want to standardise our approach to both.”
The Tardis has proved to be an asset in improving their knowledge of thermal and airtightness-related challenges – an asset which is already being shared with the other T1Cs.
Kier have constructed a Tardis at their project at Currie Community High School which replicates all of the critical airtightness and thermal interfaces. It has been invaluable for Kier and their specialist supply chain to prove performance before commencing work on the main building.
A learning journey for industry
Initial tests in the Tardis revealed small details that needed improvement, such as air gaps in window details or the duct joints. Findings from the tests were used to make modifications and improvements on where thermal bridges or air gaps were found, ensuring future projects benefit. This applies to the supply chain as well. Allan cited that everyone involved is benefiting from the feedback that the Tardis is providing.
It's not a siloed approach. Allan Smith
The impact of offsite airtightness testing
Despite the standard originating in the 1990s, delivering Passivhaus builds is still very new for the sector. Allan says it is test bays like this that give main contractors and their supply chains confidence to deliver the new wave of steel frame Passivhaus buildings in Scotland.
“It's allowing innovative solutions to be tested in controlled environments that can then be directly applied to current real-life projects and also give our supply chain that kind of in-depth understanding of how things are supposed to be.”
“It's about chasing those little 1% improvements and if you can keep making those in a testing environment then that adds up to quite a lot on site.”
Next steps
The journey of the Tardis continues as Morrison Construction plans to retest modified details and incorporate lessons learned into future projects. They have more projects they are looking to use the learnings on and Allan will be recording findings to share.
The test bay will remain a central hub for testing innovative solutions and pushing the boundaries of low carbon construction.
The influence of the Tardis is also being replicated across live sites, with project specific test mock-ups being installed, in particular on Passivhaus projects, and this reflects the increasing importance and attention to detail on quality, buildability and upskilling the workforce.
By bringing together key players, the T1C collaboration exercise has created another platform for driving quality and improvement in Passivhaus and low carbon building practices for the sector.
- Kier Construction
- Robertson
- Morrison Construction
- Morgan Sindall
- Balfour Beatty
- BE-ST